Entities
View all entitiesCSETv1 Taxonomy Classifications
Taxonomy DetailsIncident Number
30
AI Tangible Harm Level Notes
Delay & financial loss cannot be linked to the performance of the robots but is instead due to a misallocation of resources from management side.
Special Interest Intangible Harm
no
Date of Incident Year
2018
CSETv0 Taxonomy Classifications
Taxonomy DetailsPublic Sector Deployment
No
Lives Lost
No
Intent
Accident
Near Miss
Unclear/unknown
Ending Date
2018-01-01T00:00:00.000Z
Beginning Date
2018-01-01T00:00:00.000Z
Risk Subdomain
7.3. Lack of capability or robustness
Risk Domain
- AI system safety, failures, and limitations
Entity
Human
Timing
Post-deployment
Intent
Unintentional
Incident Reports
Reports Timeline
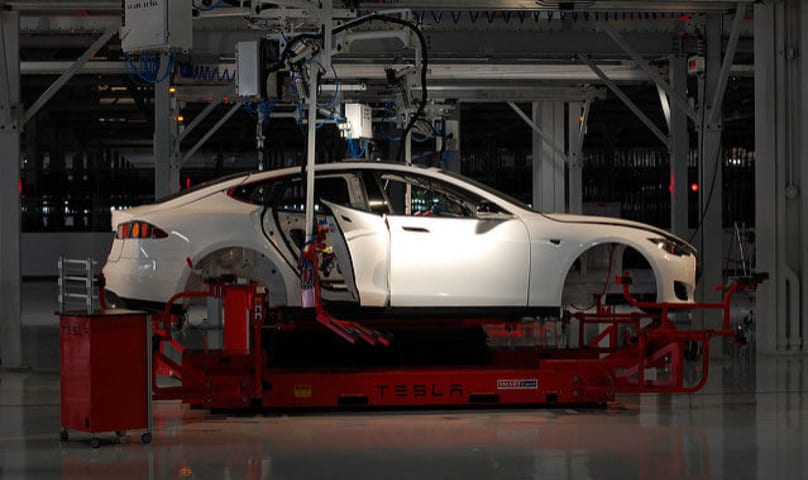
Production had been halted for much of last week in Tesla's car factory in Fremont, California, and its battery factory near Clark, Nevada. In a Tuesday note to employees, CEO Elon Musk said that the pause was necessary to lay the groundwor…

Elon Musk has said that “excessive automation” is partly to blame for the serious backlog in production of Tesla cars, noting that human beings can in some situations do a better job.
Mr Musk has come under fierce criticism for the delays f…
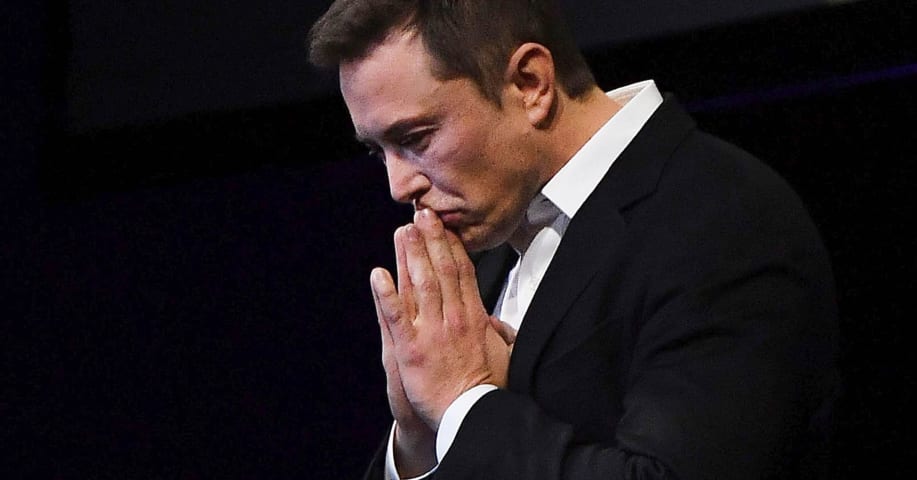
Tesla's problems with battery production at the company's Gigafactory in Sparks, Nevada, are worse than the company has acknowledged and could cause further delays and quality issues for the new Model 3, according to a number of current and…
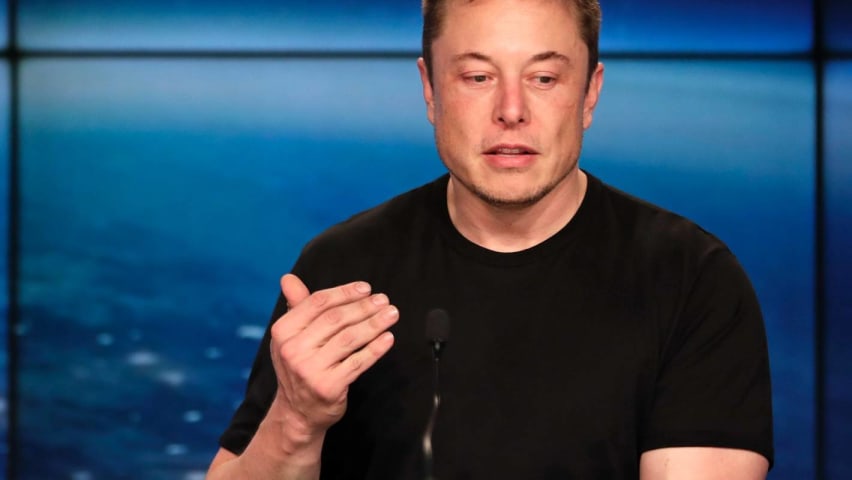
In a rare win for humans over robots in the battle for labour efficiency, Wall Street analysts have laid down a compelling argument that over-automation is to blame for problems at the billionaire Elon Musk's electric-car company.
That is t…
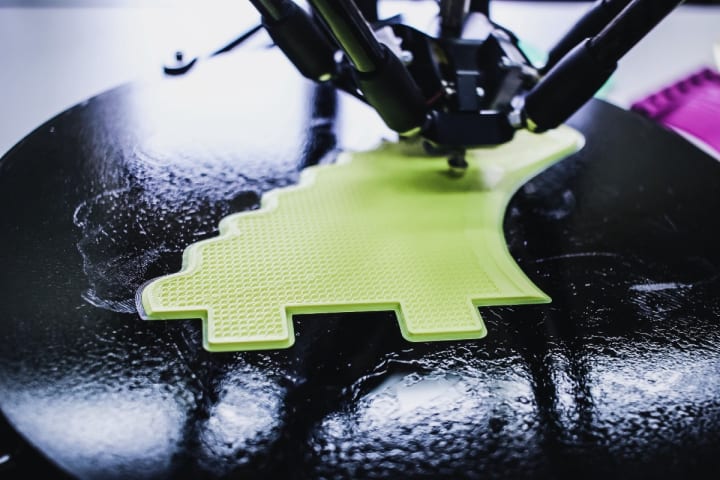
Tesla’s Factory Woes Reveals Why You Shouldn’t Automate Everything
Carlos E. Perez Blocked Unblock Follow Following Mar 29, 2018
Photo by Ines Álvarez Fdez on Unsplash
There are new reports that Tesla’s AI strategy to automate their entire …
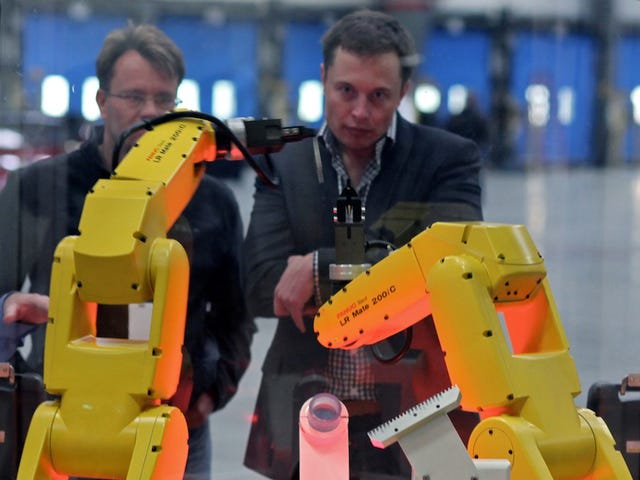
Analysts at Bernstein argue that Elon Musk has over-automated Tesla.
The very robots that Musk says will revolutionise the car industry are baking in Tesla’s mistakes and costing far more money than they’re worth, they say.
The robots are k…
Can we please replace the link with this article?
It answers why the analyst think Tesla's way of doing things is an issue:
the Japanese, try to limit automation because it "is expensive and is statistically inversely correlated to quality…
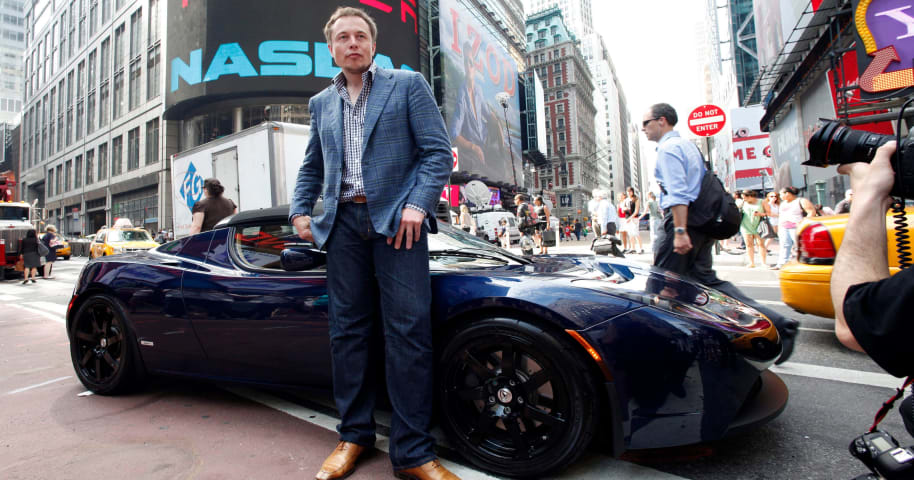
CLOSE It’s in “production hell,” according to Elon Musk Time
Elon Musk, CEO of Tesla Motors, poses with a Tesla car in front of Nasdaq following the electric automakerís initial public offering on June, 29, 2010, in New York. (Photo: Mark L…
Tesla Inc.’s Elon Musk, who’s built up an aura around how automated his car assembly plant will be, has good news for humans: We still need your help.
“Excessive automation at Tesla was a mistake. To be precise, my mistake,” the CEO wrote i…
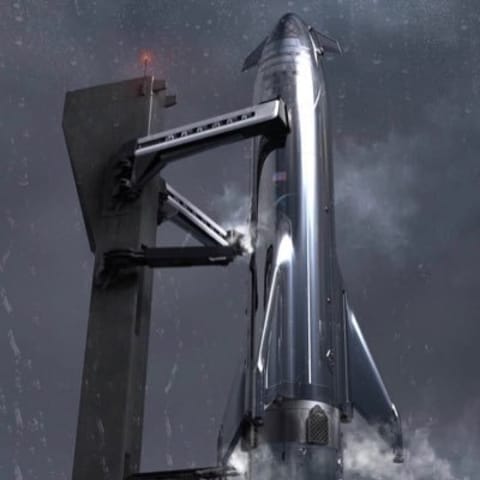
Elon Musk: "Yes, excessive automation at Tesla was a mistake. To be precise, my mistake. Humans are underrated."
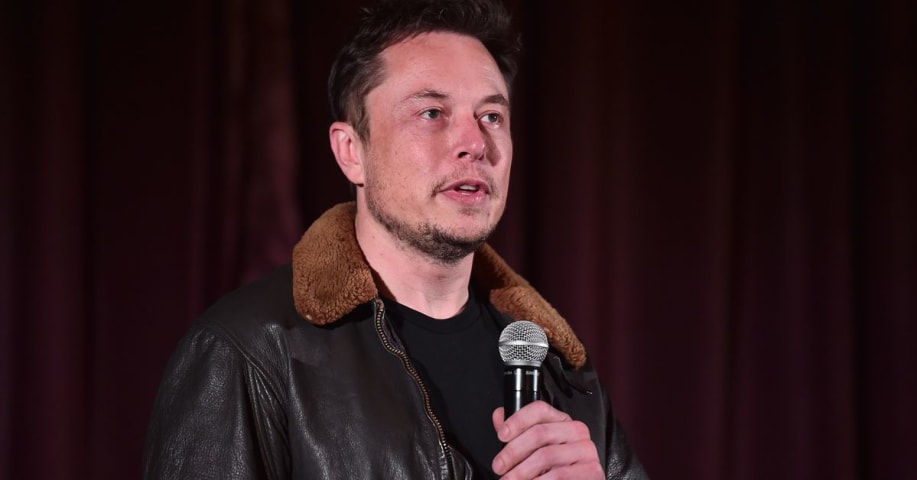
Elon Musk says Tesla relied on too many robots to build the Model 3, which is partly to blame for the delays in manufacturing the crucial mass-market electric car. In an interview with CBS Good Morning, Musk agreed with Tesla’s critics that…
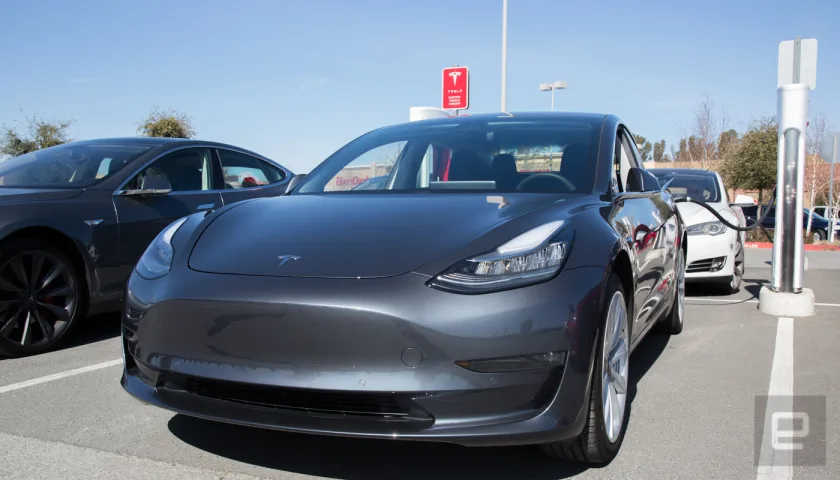
Musk didn't get to elaborate on the complexities of his factory setup, but he did point out one particular failure: the facility at one point used a "crazy, complex network of conveyor belts, and it was not working so [Tesla] got rid of the…

After Tesla failed to hit its goal of producing 2,500 Model 3 electric cars a week, CEO Elon Musk says he's figured out what went wrong: robots.
Yes, robots, which are designed to help build lots and lots of Tesla's electric vehicle at an i…
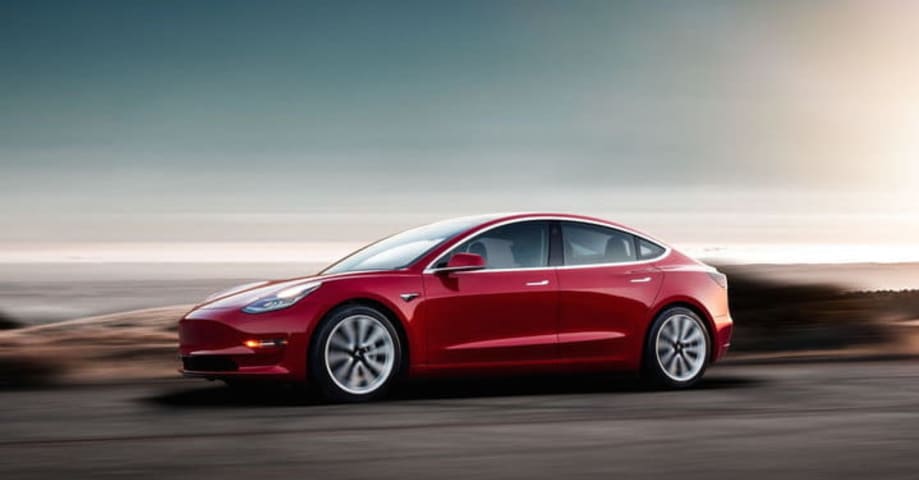
Share
In a recent interview with CBS, Elon Musk discussed the future of Tesla and the problems the manfucturer was having producing enough Model 3 vehicles to meet growing demand. One of the issues that Musk touched on was the company’s ove…

NON-ALIEN Elon Musk has agreed with critics who say that Tesla is overly-reliant on automation and has too few human assembly line workers building the Model 3.
During an interview with CBS, Musk said that using too many robots in the produ…
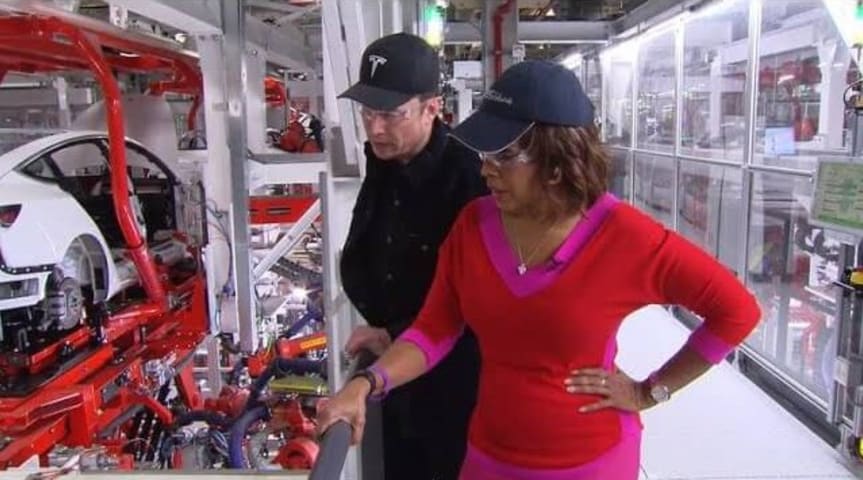
After missing its target of producing 2,500 Model 3 cars per week at the end of Q1 2018, Tesla CEO Elon Musk has revealed what went wrong: battery production problems – plus too many robots on the production line.
While the production of th…
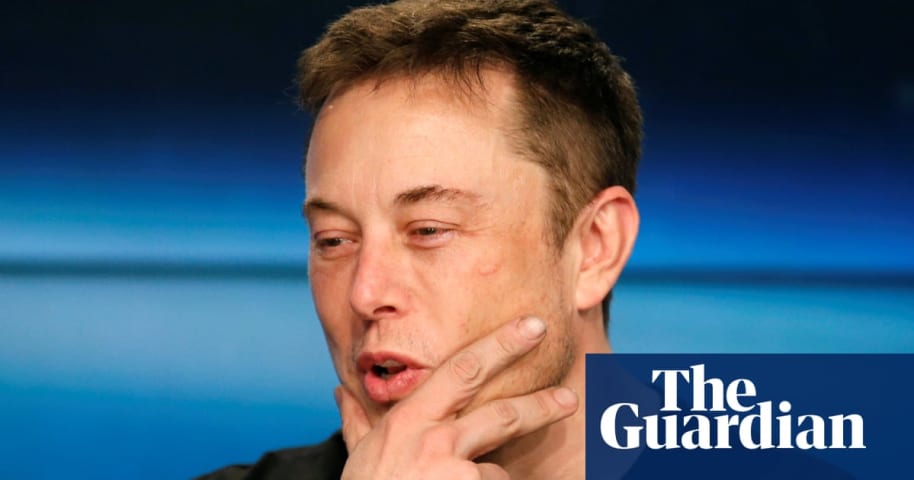
‘Humans are underrated,’ says CEO after company failed to hit weekly production target in first quarter of 2018
This article is more than 11 months old
This article is more than 11 months old
Elon Musk has admitted that automation has been …
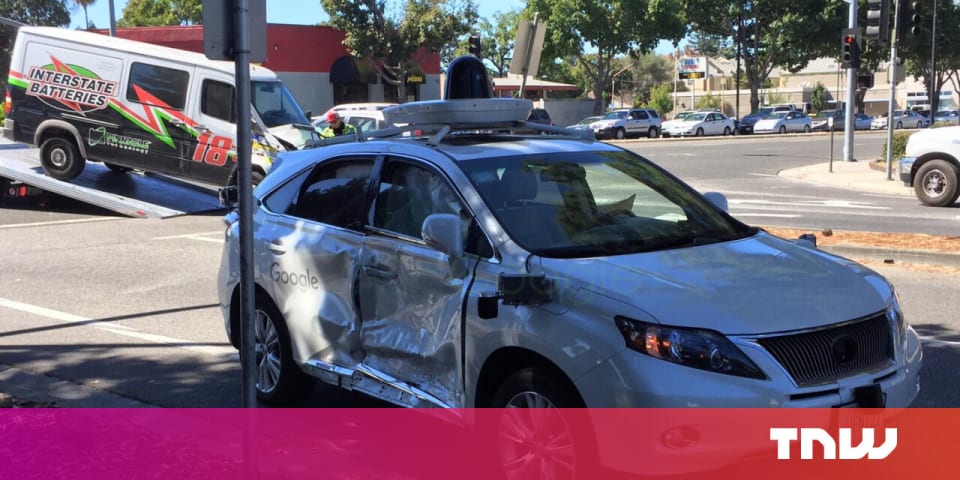
In a delicious turn of fate Elon Musk has put robots the world over on notice. He recently replaced the highly-touted automation system at Tesla with a better, more intelligent paradigm: humans.
Tesla’s Model 3 production facility is regard…
Tesla’s new Model 3 car is seen Jan. 26 at the Tesla store in Washington. (Salwan Georges/The Washington Post)
For the second time since February, Tesla said Monday it has temporarily suspended production of its Model 3 sedan, a move that a…
(Reuters) - Tesla Inc (TSLA.O) shares fell as much as 2 percent in premarket trading on Tuesday, a temporary halt in production of its Model 3 sedan adding to nerves about the electric car maker’s consistent failure to keep its promises on …
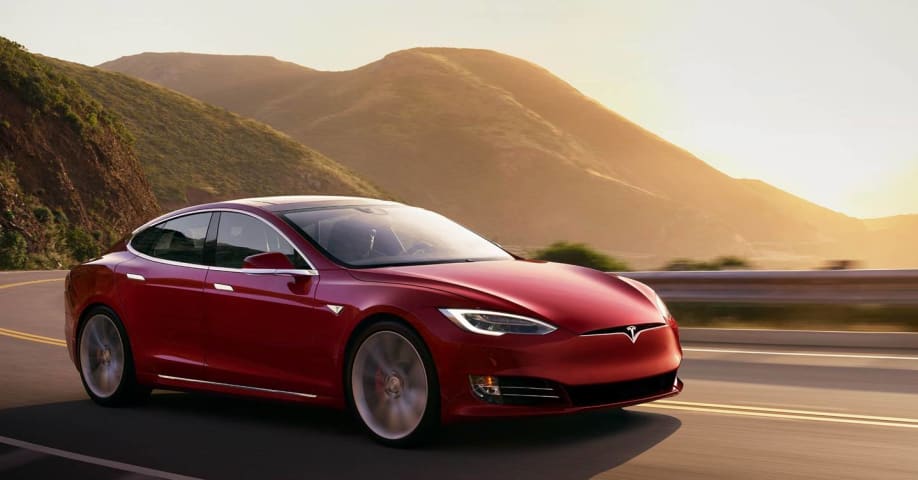
Tesla
Elon Musk looks tired. There are bags under his eyes and an embattled admittance of disappointment has replaced the billionaire entrepreneur’s typical exuberance. A big, yellow strapline reads "PRODUCTION HELL" and CBS This Morning co…
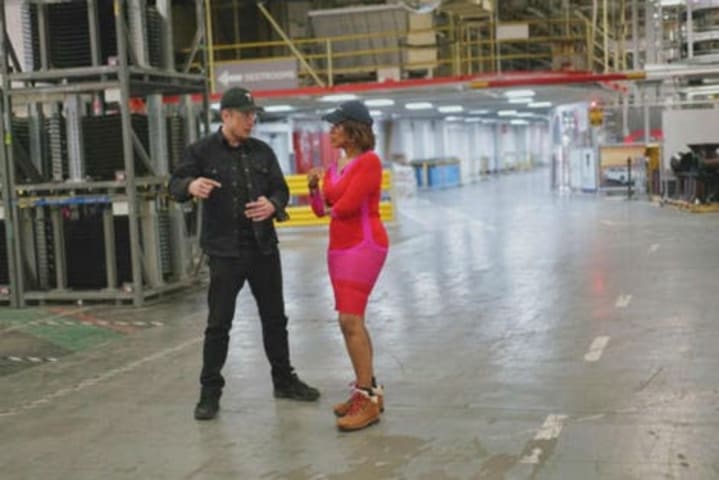
CBS This Morning
In a push to deliver cars to waiting customers, Tesla is moving to 24-hour operations at its Fremont, California, assembly facility and plans to hire "400 people per week for several weeks" between Fremont and its battery G…
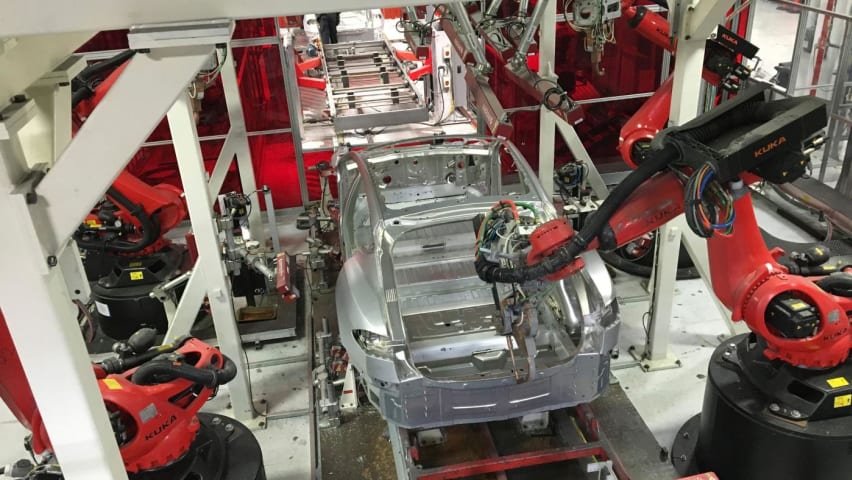
Investors and fans of Tesla are anxious to hear what the company has to say about the production ramp of the Model 3, the main driver of future profits and cash-flow, when it releases its first-quarter results on May 2.
Analysts at Bernstei…
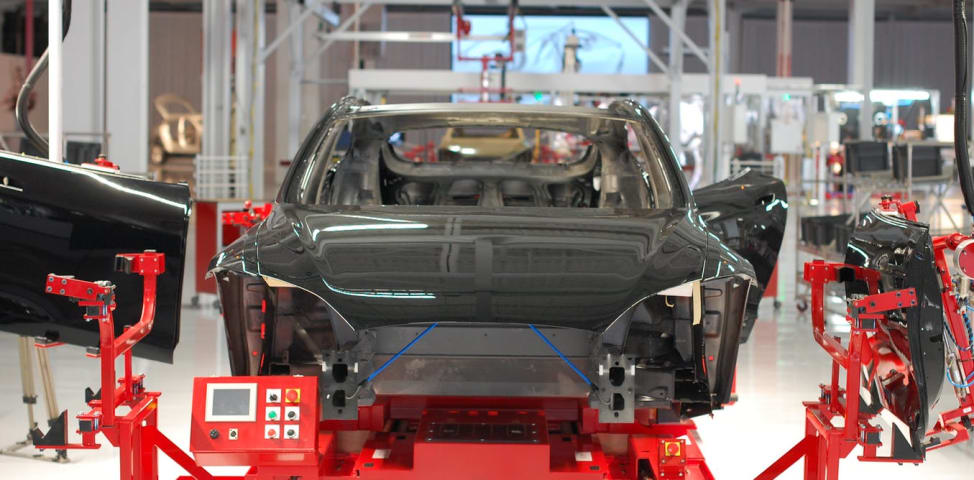
Tesla was hoping to produce 5,000 new Model 3 electric cars each week in 2018. So far, it has failed to manufacture even half that number. Questioned on the matter, the company’s CEO, Elon Musk, claimed that “excessive automation was a mist…
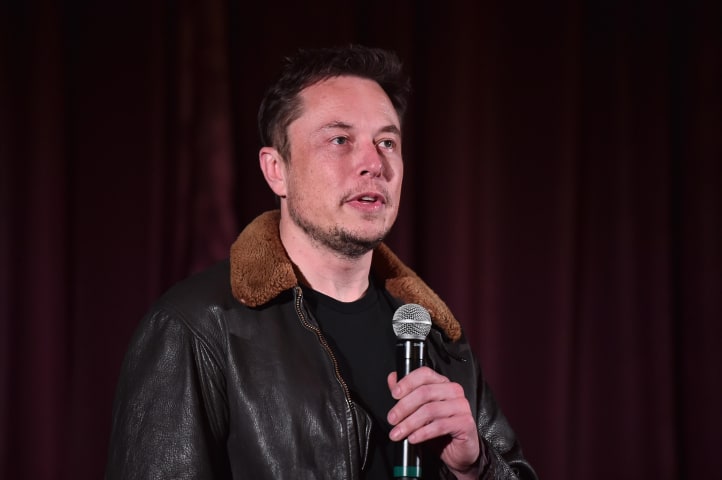
Flufferbot! Alberto E. Rodriguez/Getty Images
Falling behind production deadlines for its Model 3 sedan and rapidly burning cash, Tesla has been struggling mightily to speed up its assembly line. On a call with investors Wednesday, CEO Elon…

Elon Musk has six days to make good on his pledge that Tesla will be pumping out 5,000 Model 3 sedans a week by the end of the month. If he succeeds, it may be thanks to the curious structure outside the company’s factory. It’s a tent the s…
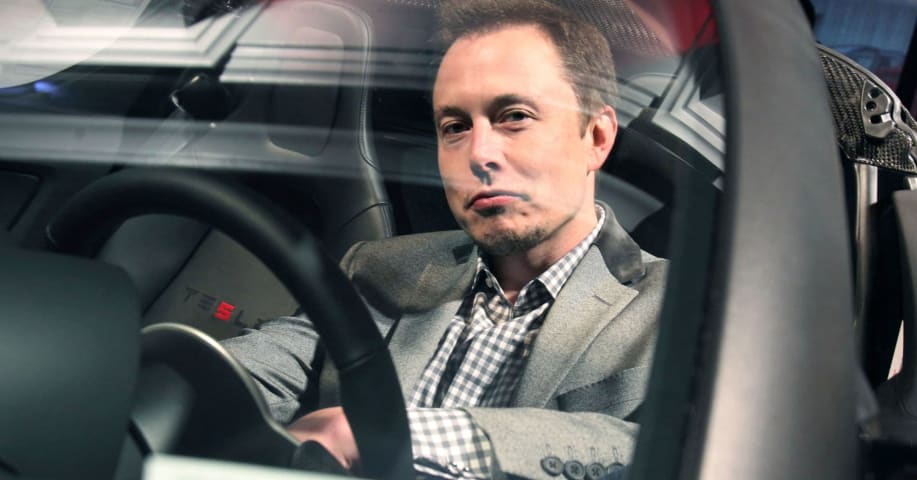
Tesla's future as a mass-market car company hinges on efficient, automated production of the Model 3. Tesla will lose $6,000 for every $35,000 Model 3 it sells, says UBS analyst Colin Langan. It only breaks even if the car sells for over $4…
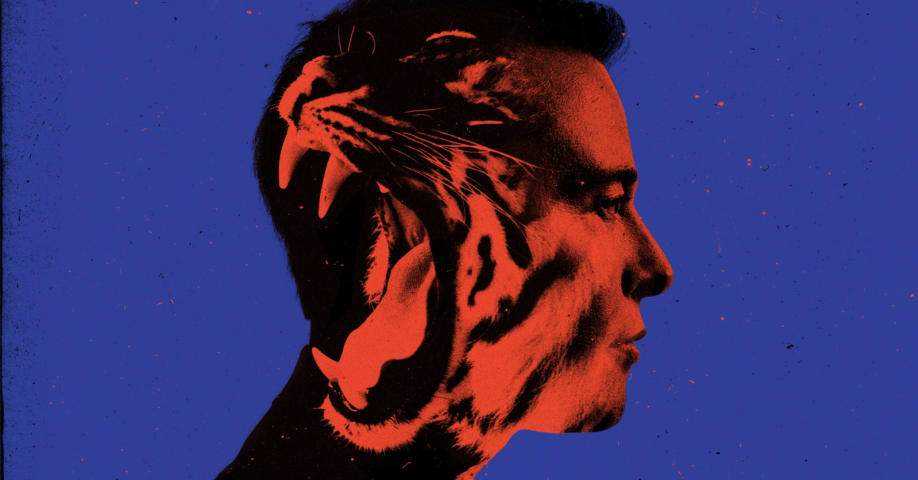
The young Tesla engineer was excited. Ecstatic, in fact. It was a Saturday in October 2017, and he was working at the Gigafactory, Tesla’s enormous battery manufacturing plant in Nevada. Over the previous year, he had been living out of a s…
Variants
Similar Incidents
Did our AI mess up? Flag the unrelated incidents
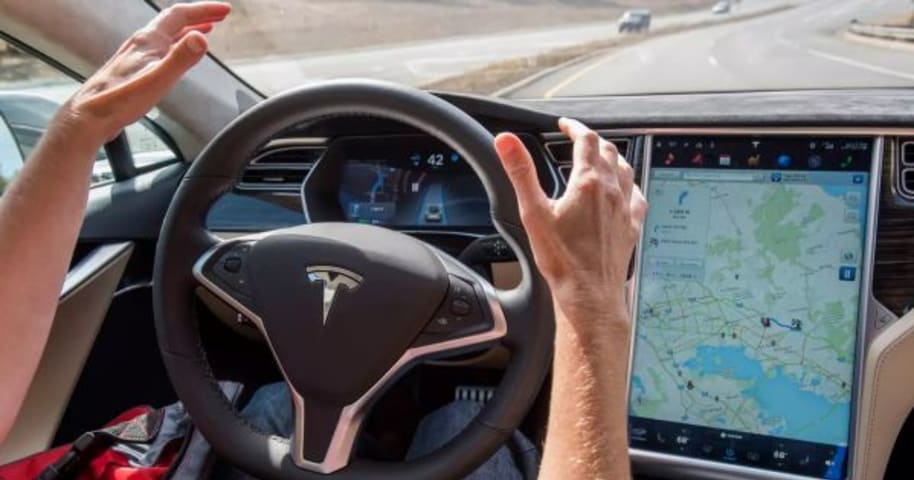
A Collection of Tesla Autopilot-Involved Crashes
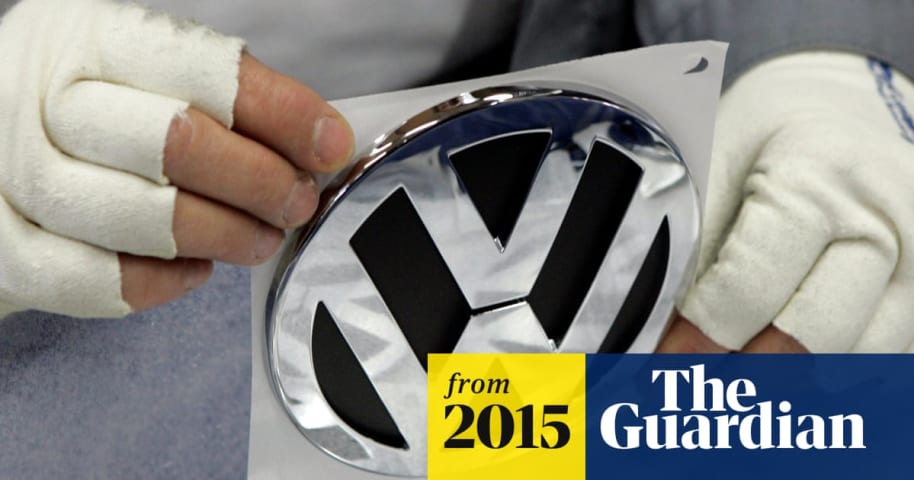
Robot kills worker at German Volkswagen plant

Near-miss between two Self-Driving Cars
Similar Incidents
Did our AI mess up? Flag the unrelated incidents
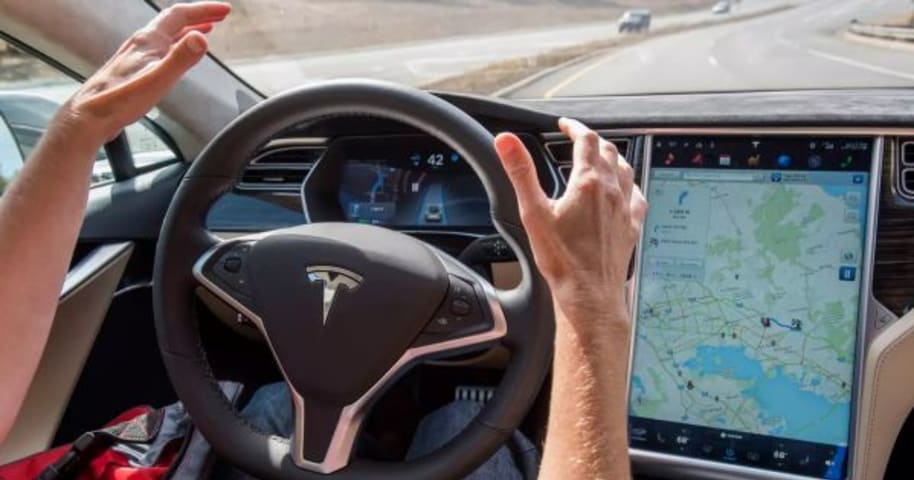
A Collection of Tesla Autopilot-Involved Crashes
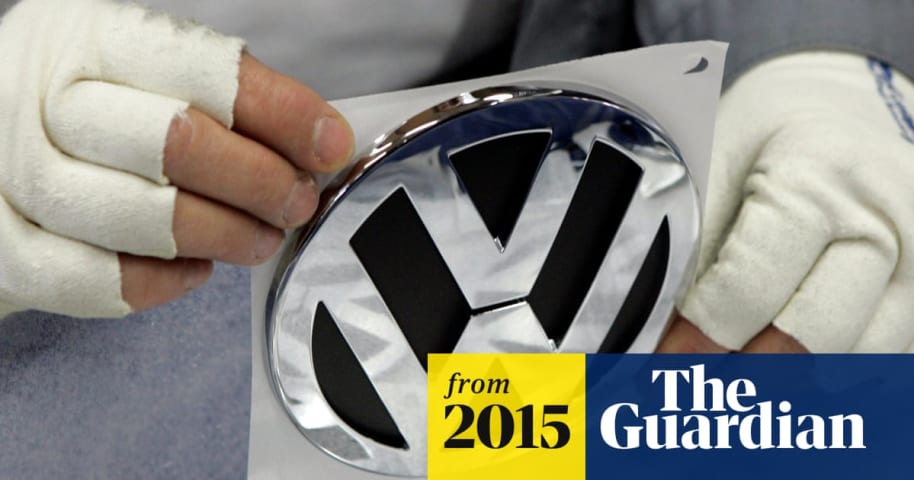
Robot kills worker at German Volkswagen plant
